For many years, reflective sheeting has been utilized to make persons and objects more visible. Due to its composition of tiny glass beads that reflect light, it makes it simpler for drivers to see objects at night or in low light. Yet, what precisely is reflective sheeting and how is it produced? In this blog post, we’ll examine the production of reflective sheeting in more detail and go over some of the crucial steps.
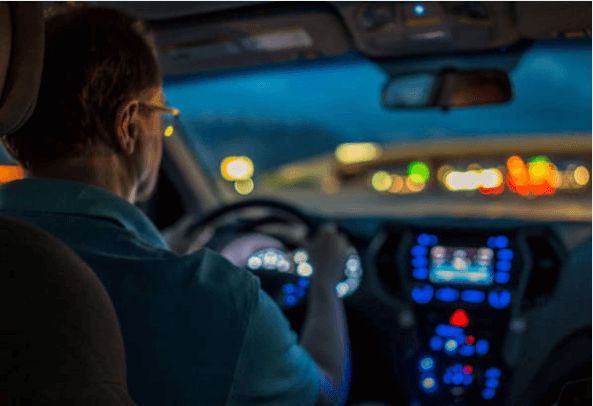
What reflective sheeting is used for?
A substance used to reflect light is reflective sheeting. Traffic signs, temporary construction zones, automobile decals, license plates, safety jackets, footwear, and other fashionable clothes frequently employ it. Because it contains small glass beads that bounce light back to the source, reflective sheeting is reflective. Light is returned in a straight line after striking the beads’ reflective surface. As a result, the reflective sheeting is particularly noticeable at night or in low light. Reflective sheeting is a crucial safety measure since it improves visibility for both cars and pedestrians in low-light situations. Reflective material can also be utilized to add style. For example, many people use reflective sheeting to decorate their cars or to make their clothing more visible in nightclubs or at night. Reflective sheeting is a versatile product that has many uses.
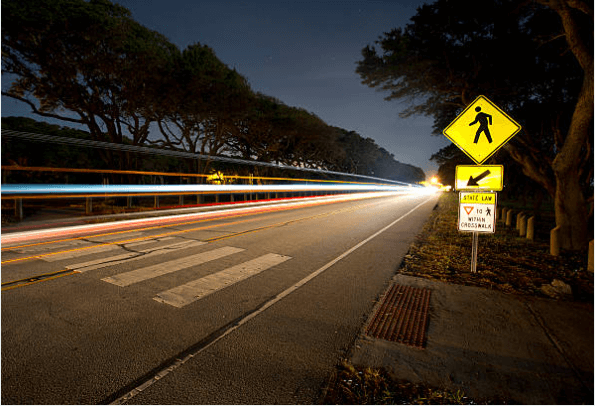
What is reflective sheeting made of?
It is often constructed from a mixture of many film layers consisting of materials like PET, PVC, PMMA, and PC. The reflective layer, which can be constructed of either microprisms or tiny glass beads, is what gives the sheeting its reflecting features. In opposed to microprisms, which can be either corner cube or whole cube prisms, glass beads are normally enclosed or encapsulated. The reflectivity of the sheeting can be significantly influenced by the material and type of reflector employed.
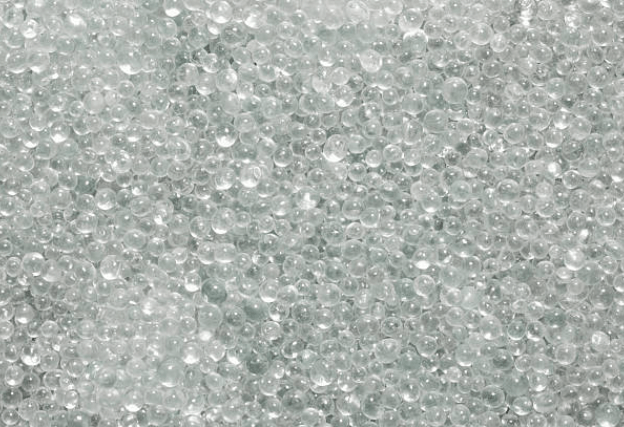

What is the best material for reflective sheeting?
For the durability and reflectivity perspective, normally people think the best material for the face film is PMMA, which could let more light in and out and more durable, the disavantage of PMMA is it is the most expensive. So, for the reflective sheeting doesn’t require high reflectivity and lifetime, people will use PET or calendered PVC, just to save the cost.
Since now more modifed materials are used in reflective sheeting to meet different customer’s needs, it is hard to say which one is the best.

Beads or prism?
Yes, reflective sheeting could be devided into two types by structure, glass beaded type and prismatic type, which indicate the method the reflect the light.
Reflective sheeting is used for a variety of purposes, from reflective pavement markings to reflective clothing. It is made from a variety of materials, but most commonly from glass beads or prisms. Each type has its own advantages and disadvantages.
Glass bead reflective sheeting is more flexible and embossable than prismatic reflective sheeting. However, it is not as reflective and has symmetrical reflectivity (no difference when measured by different angles). It is also lower cost than prismatic reflective sheeting.

Compared to glass bead reflective sheeting, prismatic reflective sheeting is more reflective. It isn’t as flexible or embossable, though. Moreover, it displays asymmetric reflectivity (meaning that it reflects light differently when measured by different angles). Additionally more expensive than glass bead reflective sheeting is prismatic reflective sheeting.

Which one is more eco-friendly?
Prismatic sheeting is considered to be more eco-friendly because it is manufacutred with less manufacturing process, and use less liquid solvent(means less VOC emission, and less energy consumption, and longer service time(No need to replace so frequently).

Price? How much does reflective sheeting cost?
Depending on the style, size, and amount you require, reflective sheeting might range in price. For instance, a roll of prismatic reflective sheeting may run you about $60, but a roll of glass bead reflective sheeting might cost you about $30.
Unless they are specifically created to meet the needs of a particular consumer, beaded products are often less expensive than prismatic ones.
According to the market, the cost of reflective sheeting may range from 0.3 to 4 USD per square foot.

What is the structure of reflective sheeting?How many layers.
Just check the below 3D animation: It has multiply layer include, face film, reflective layer, adhesive, liner.

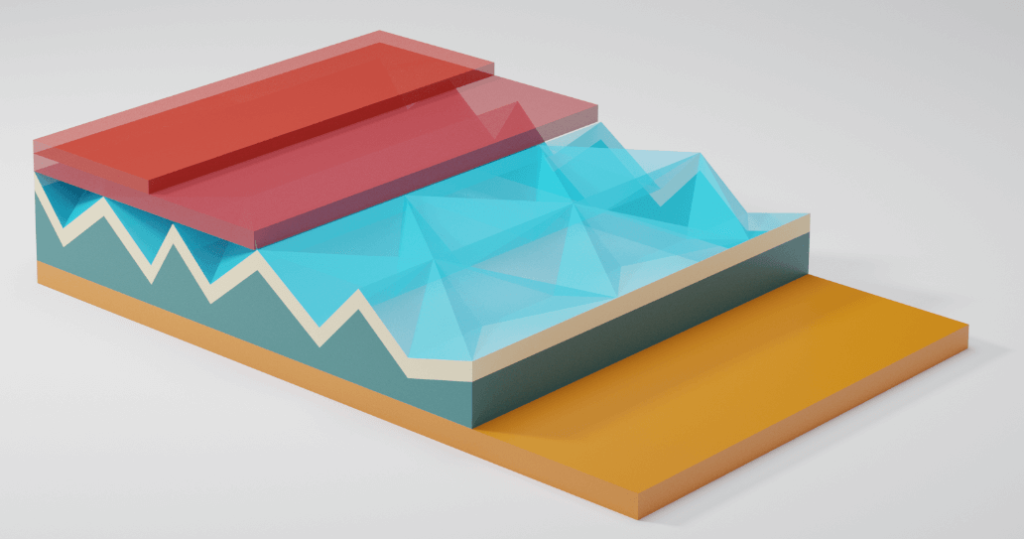
Why it need so many layers?
In order to reflect light, reflective sheeting is frequently utilized in a variety of scenarios. For instance, it is frequently used on traffic signs and on the clothes worn by construction workers and bikers that is reflective. Even while reflective sheeting normally just has a few millimeters of thickness, it actually has several layers. The reflective sheeting is more effective thanks to the cooperation of these layers, which have various purposes. Typically, translucent plastic forms the top layer, allowing light to travel through. The reflective layer that lies beneath this one reflects light back up through the clear layer. The reflective sheeting is next coated with an adhesive coating, which helps secure it to the surface it is being applied to. Each of these layers is crucial to the ability of reflective sheeting to effectively reflect light. Reflective sheeting would not be nearly as effective at reflecting light without all three layers.

The face film
When formed with a different material, it can be more resistant to sunlight and serve as a protective coating against water and dirt. The face film can also function as a printing surface for graphics or other information. It can also be colored by applying common colors like yellow, red, green, blue, orange, or brown to these layers. To improve strength or barrier qualities, the face film may occasionally be bonded to another layer.
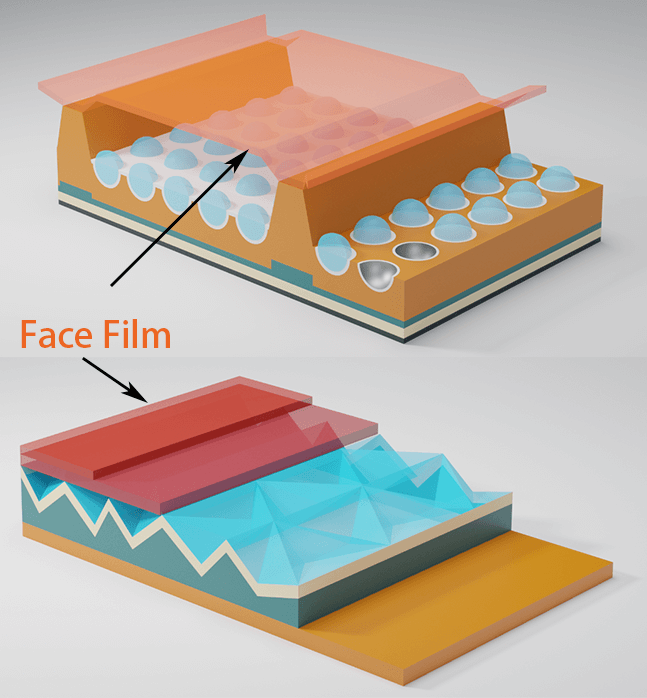
Reflective layer
The reflective layer is the core element of all reflective sheeting. It is responsible for reflecting light back to the light source. This layer is made up of beads or prisms, which can be divided into metallic and non-metallic types. Metallic reflective materials use alluminium galvanized layer to reflect light as a mirror do, while non-metallic materials use air-backed layer to reflect light. Both types of materials are effective at reflecting light, metallic materials typically have a higher reflectivity, while non-metallice material has more vivid colors. The type of reflective material used will depend on the intended application. For example, overhead traffic signs often use non-metallic reflective sheeting because it is more color contrast. However, non-metallic materials are often used for applications where durability is more important, such as on conspicuity tape and temporary workzone signs where the working conditions are not good.

Ahesive
It is gennerally pasted with permanent presure sensitive adhesive to meet the application need of reflective sheeting, reflective sheeting could only stuck on the surface with it. However, many other adhesives are available that provide different degrees of stickiness, sheen, and permanence. Some adhesives are water-based, while others are solvent-based. The type of adhesive you use will depend on the project you are working on and the materials you are using. If you are unsure which adhesive to use, consult with a professional before beginning your project. Whatever adhesive you choose, be sure to read the instructions carefully and test it on a scrap piece of material before proceeding.

Liner
A liner is a thin layer of material used to protect opposite surface from adhesive. It is used in many different industries, from construction to manufacturing. Liners are typically made of paper, plastic, and pasted with silicon oil, which make it has low releasing force. They are applied to the surface before the adhesive is applied. This prevents the adhesive from sticking to the surface before to be used. Liners can also be easily peeled off when they are no longer needed. This makes them an essential part of many different types of projects. without a liner, adhesive can cause serious damage to surfaces. That’s why liners are such an important part of many different types of projects.

How are the reflective sheeting’s layers compounded?
The layers of reflective sheeting are assembled using a production line and a variety of machines. Machines for coating, extrusion, lamination, and other processes might be used in this production line. They are all employed to combine various layers into a single film. The reflective sheeting is then shaped and sized to perfection. This procedure is crucial for producing a product that will be long-lasting and efficient. To be visible by drivers, the reflective sheeting needs to be weatherproof and reflect light. The layers can be compounded to produce a final product that satisfies all of these criteria.

The manufacturing process of reflective sheeting
A substance used to reflect light is reflective sheeting. It is constructed from reflecting particles that are joined by a binder. Glasses, metal, or polymer can all be used to make the reflecting particles. Vinyl, PET, or acrylic may be used as the binder. The reflective particles and binder are first combined to create reflective sheeting. After that, the mixture is put on a set of rollers and sent through an oven. The binder melted as a result of the mixture being heated in the oven. The reflective particles are joined together by the melted binder. The reflective sheeting is cut into sheets and rolls once it has cooled. Several products, including reflective tape, reflective signs, and reflective clothing, use reflective sheeting.
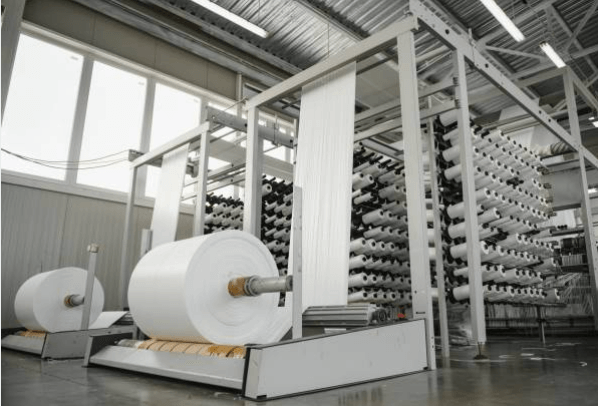
How to select the right type of reflective sheeting for your needs?
If you are in the market for reflective sheeting, there are a few things you need to keep in mind in order to select the right type of product for your needs.
First, The three most common types of reflective sheeting are engineer grade, high intensity and diamond grade. Engineer grade reflective sheeting is the most economical option and is typically used for sign making. High intensity reflective sheeting is more expensive but offers a higher level of reflectivity. Diamond grade reflective sheeting is the most reflective option but is also the most expensive.
Second, because reflective sheeting is available in lots of colors, you must choose the one that writen on your local standard at night or in low light. Finally, there are several thicknesses of reflective sheeting available, so you must decide how thick of a layer you require to obtain the desired level of reflectivity.
Last but not least, reflective sheeting can be attached to a number of surfaces, so you need to choose the adhesive type that will work best with the material you intend to use. You may choose the proper kind of reflective sheeting for your needs by keeping these things in mind.

Installation tips for reflective sheeting
Reflective sheeting can serve to increase the visibility of traffic signs, which are an important component of our roads, particularly at night in inclement weather. A thin layer that can be applied to both rigid and flexible sign materials is reflective sheeting. Although it comes in a range of hues, white and yellow are by far the most popular. Sign faces must be fully clean and dry before applying reflective sheeting; otherwise, the sheeting won’t stick to the surface correctly. Before exposing the sign to traffic, the reflective sheeting should have had a chance to dry for 24 hours. Reflective sheeting should be changed at least once every five years for best results.

Care and maintenance of reflective sheeting?
A material that reflects light is called reflective sheeting. It is parts of reflective materials family and broadly used on traffic signs. For reflective sheeting to function properly, it must be kept spotless and clear of debris. In order to prevent damage to reflective sheeting, it is also crucial to preserve it carefully. Befor e application, reflective sheeting should be kept in a cool, dry location away from direct sunlight. Moreover, reflective sheeting needs to be kept out of reach of heaters like stoves and furnaces. To ensure that reflective sheeting continues to reflect light properly, it should be replaced right away if it sustains damage.

Common problems with reflective sheeting and how to fix them?
The reflective sheeting on traffic signs can get broken or damaged over time, which is one of the most frequent issues. Many factors, such as exposure to the sun, extremely high or low temperatures, or even physical injury, can cause this. There are a couple fixes you can make if the reflective sheeting on your traffic sign is broken or damaged. Start by wiping the sign down with a soft cloth and some soapy water. If this doesn’t work, you can try covering the cracks with reflective tape. Last but not least, you can always change the reflective sheeting on your sign if everything else fails.
Reflective sheeting’s potential to rip off the surface it is put on or to deteriorate over time is another issue. Use a clear laminate over the reflective vinyl or a clear lacquer over the reflective glass beads to solve these issues. The previous coating of reflective vinyl or glass beads can also be covered with a fresh one.
